Beschreibung
Beschreibung
Kurzbeschreibung
Wir lösen die Probleme der Industrie in der Verbindungstechnik. Insbesondere Metall-Kunststoffverbindungen werden immer häufiger benötigt, um schweres Metall durch leichten Kunststoff zu ersetzen. Aktuell werden solche Verbindungen durch Nieten oder Schrauben realisiert. Unsere Technologie - das Nanoscale Sculpturing - optimiert diese Verbindungen oder ermöglicht sie erst: Wir machen Produkte haltbarer, leichter und kostengünstiger.
Dagegen weisen die herkömmlichen Methoden deutliche Nachteile auf: sie sind schwerer, meist nur händisch umsetzbar und ihre Verarbeitung wird z.B. bei komplexen Geometrien schwieriger und damit teurer. Manche Materialkombinationen funktionieren auch schlicht und einfach nicht.
Kleine Struktur, große Wirkung. Durch unser Nanoscale Sculpturing erzeugen wir auf dem chemischen Weg kleinste Hinterhakenstrukturen, mit denen sich Kunststoffe, Kleber oder Lote verbinden. Darüber hinaus erreichen wir durch die 3 dimensionale Strukturierung nahezu eine Verdopplung der verfügbaren Verbindungsfläche.
Das Ergebnis: bis zu 5x festere, langlebige Verbindungen als bei herkömmlichen Verfahren und die Möglichkeit durch gezielte Materialkombinationen verbesserte Funktionalität zu schaffen (bessere Wärmeabfuhr, Dichte, elektrische Leitfähigkeit, Beständigkeit bei starken Temperaturschwankungen, etc.). Durch die geringe Strukturtiefe sind Werkstücke zudem einfach zu recyceln.
Unsere Kunden kommen aus den Bereichen Automobil, Luftfahrt und Schiene. Für diese Branchen werden wir Metall-Strukturierungen in großen Stückzahlen als Fremdfertigung realisieren oder Anlagentechnik, insbesondere als mobile Lösung, anbieten. Unsere Prozesse sind komplett automatisiert – und unsere Kunden müssen ihre Abläufe nicht ändern, es sei denn, sie werden drastisch vereinfacht. Unsere Technologie lässt sich hervorragend auch auf dünnsten Folien realisieren und eignet sich daher auch ideal zum Einsatz in nachhaltigen Batteriekonzepten.
In einem geförderten Projekt konnten wir mit der Universität Kiel einen ersten Demonstrator einer grünen, explosionssicheren und leistungsstabilen Schwefel-Silizium-Batterie herstellen. Durch die optimierte Anbindung des Aktivmaterials können wir sowohl heute bekannte Batteriekonzepte verbessern, sowie zukünftig neuartige realisieren.
Wir konnten in unseren bezahlten Kundenprojekten zeigen, dass das Nanoscale Sculpturing nicht nur im Reagenzglas im Umfeld der Universität funktioniert, sondern auf reale Produkte Anwendung findet. Mit ersten Demonstratoranlagen haben wir gute Strukturierungsergebnisse u.a. bei Folien erzielt. Aktuell werden sie zu Prototypen entwickelt, damit zeitnah die Serienfertigung gestartet werden kann.
Über die nascit GmbH
2019 gegründet und 2021 gestartet, als technische Ausgründung aus der Kieler Universität, arbeiten wir bei nascit an der Verbindungstechnologie von morgen. Mit unserer chemischen Oberflächenbehandlung für Metalle schaffen wir die Grundlage für feste und langlebige Verbindungen von Metall und Kunststoff.
Aktuell überführen wir die Anwendungsentwicklung unserer Kunden in konkrete Serienaufträge und Anlagenentwicklung. Hierbei kommen die Kunden, zumeist Top-DACH-Unternehmen mit ihren Problemen auf uns zu.
Team
Karsten Wenige
Geschäftsführer und Gründer
Dr. Ing. Henning Winterfeld
Technischer Leiter
(v.l. Dr. Ing Chima Kalu, Jakob Offermann, Dr. Ing. Henning Winterfeld, Karsten Wenige, Ibrahim Kassem)
Chima und Jakob arbeiten bei uns an der Prozessentwicklung und sind unser Garant dafür, dass nur beste Werkstücke zum Kunden gelangen. Ibrahim arbeitet als Maschinenbauer an der Überführung der Prozesse und Methoden in Anlagenkonzepte, um die Skalierung unseres Prozesses zu ermöglichen.
Innovation
Mit dem an der Kieler Universität entwickelten Nanoscale Sculpturing Verfahren bearbeiten wir die Oberflächen von Metallen chemisch, um die Oberfläche um das Zweifache zu vergrößern und mikroskopisch kleine Hakenstrukturen zu erzeugen. Mit dieser besonderen Metalloberfläche lassen sich Kunststoffe fest und permanent verbinden. So realisieren wir neue Metall-Kunststoff-Hybridbauteile und ermöglichen unseren Kunden ihre Produktionsprozesse und Produkte zu verschlanken und neue, bisher unmögliche Produktkonzepte zu realisieren.
Abbildung: Vergleich zwischen Laser-Vorbehandlung (links) und unserem Nanoscale Sculpturing (Mitte). Insbesondere die Hakenstrukturen (exemplarisch rechts dargestellt) ermöglichen die starken Verbindungen.
Die Einsatzmöglichkeiten unseres Nanoscale Sculpturing Verfahrens finden sich fast überall dort, wo Verbindungstechnik gebraucht wird. Aktuell fokussieren wir uns auf den Mobilitätssektor, da dort der Innovationsdruck besonders groß ist.
Über die reine Befestigung von Kunststoff an Metall hinaus bieten Verbindungen auf Basis unseres Nanoscale Sculpturing viele Vorteile. So lassen sich durch den Verbund thermisch und elektrisch leitfähige Verbindungen einfach realisieren.
Dies ermöglicht es uns auch, Aktivmaterial von Batterien effizienter an die Stromleiter anzubinden und somit nicht nur neue, grüne Batteriekonzepte zu realisieren, sondern auch bestehende in ihrer Effizienz zu steigern.
Nanoscale Sculpturing
Unsere Innovation, das Nanoscale Sculpturing, ist Basis unserer Produktpalette. Wir bieten es unseren Kunden in zwei Produkten an:
-
Unser Kernprodukt ist die Strukturierung von (beigestellten) Halbzeugen und Materialien (Metall-Folien, -Bänder, -Bleche) als Dienstleistung in Form der Fremdfertigung. Diese erfolgt zumeist in großen Stückzahlen/Mengen. Nach Strukturierung und Qualitätskontrolle unsererseits werden die strukturierten Güter dem Kunden zugeleitet. Dieser verarbeitet sie dann, wie gewohnt oder per optimiertem Prozess, ohne weiteren Aufwand oder Ausbau seiner Produktionslinie, weiter. Die Strukturierung erfolgt auf unseren entwickelten Anlagen.
-
Der Absatz von (mobiler) Anlagentechnik zur (punktuellen) Strukturierung von Metalloberflächen ergänzt unsere Strukturierungsdienstleistung. Hier sind derzeit drei wesentliche Produktansätze im Fokus: a.) Anlagen zur Endlosschienenverlegung (Bahn), b.) mobile Reparaturanlagen (Strukturierung und Verklebung) für Flugzeuge und c.) Strukturierungsanlagen für Befestigungen in engen Räumen (z.B. Bootsrümpfen).
Flankierend zu diesen Produkten bieten wir Beratungsleistungen zur Anwendungsentwicklung und das Anlagenservicing an. Insbesondere im Bereich der Anwendungsentwicklung konnten wir bereits namenhafte Unternehmen aus der DACH Region für bezahlte Projekte gewinnen. Zur Zeit entwickeln wir mit diesen Kunden schlankere und effizientere Kühlsysteme, welche weniger Materialeinsatz und einfachere Produktionsprozesse ermöglichen. Unsere Technologie erlaubt zudem sehr platzsparende und kosteneffiziente Designs.
Alleinstellungsmerkmale
Unser Nanoscale Sculpturing ist ein Game-Changer in der Verbindungstechnik. Unser Verfahren verdoppelt die Verbindungsoberfläche und arbeitet gezielt mikroskopisch kleine Hinterhaken heraus. So ermöglichen wir eine Festigkeit, Dichte und Langlebigkeit, die sonst nur von Schrauben, Bolzen oder Nieten abgebildet wurde. Allerdings sind letztgenannte deutlich prozess-, material- und damit kostenintensiver. Im Vergleich zu den bisherigen Klebeverfahren als Verbindungstechnik, halten unsere Verbindungen bis zu 5x fester.
Unser Verfahren löst darüber hinaus die Probleme komplexer Geometrien und besonders dünner Materialien. Da es ohne schädlichen Wärmeeintrag auskommt, können wir Verbindungen realisieren, die durch andere Verbund-vorbereitende Methoden (z.B. Lasern) nicht umgesetzt werden können.
Unter diesen Voraussetzungen kamen unsere Kunden mit ihren Problemen im Produktdesign auf uns zu. So können sie mit uns nicht nur Neuprodukte entwickeln, sondern auch bestehende Produkte deutlich effizienter gestalten.
Abbildung: Querschnitt einer Verbundstruktur von Aluminium und Kunststoff, welche gut den mechanischen Verbund der Materialien zeigt (links). Die Verbindung hält starker Belastung stand (rechts).
Geschäftsmodell und Vertrieb
Wir bieten unseren Kunden den Einsatz unserer Technologie in ihren Produkten über zwei Wege an.
Fremdfertigung: In diesem Bereich treten wir als Dienstleister auf und bearbeiten die Metallkörper nach den Wünschen unserer Kunden. Mit diesen Metallkörpern können die Kunden vor Ort, ohne große Anpassung des eigenen Produktionsprozesses die finale Bearbeitung ihrer Produkte vornehmen.
Anlagentechnik: In besonderen Fällen verlangt der Kunde nach speziell entwickelter Anlagentechnik, um unser Nanoscale Sculpturing Verfahren entweder bei sich vor Ort in der Produktion oder als mobile Anwendung einzusetzen. Hier entwickeln wir die Anlagentechnik nach dem Bedarf unserer Kunden und stellen Ihnen diese mit einem entsprechenden Servicing zur Verfügung.
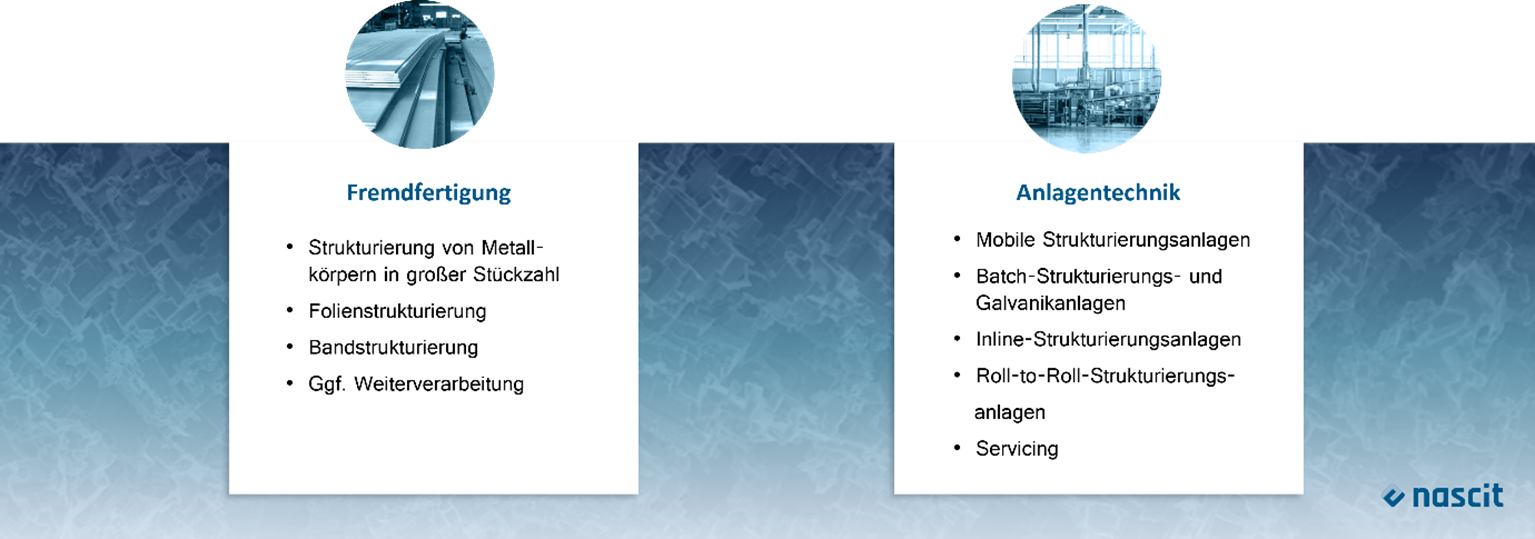
Mit der Industrialisierung und globalen Vermarktung des Nanoscale Sculpturings ermöglichen wir unseren Kunden lösungsorientierte Produktdesigns, die sich durch eine revolutionierte Verbindungstechnik den Herausforderungen der Zukunft stellen – leichter, multifunktional und kostengünstiger für die Produkte von morgen. Mit unseren Produkten setzen wir hier die Grundlagen:
Von der bezahlten Anwendungsentwicklung, über die Prototyp-Fertigung und Bemusterungen stellen wir in der Fremdfertigung unseren Kunden seriell strukturierte Werkstücke zur Verfügung. Diese werden in der Regel in großen Stückzahlen von unseren Kunden abgenommen. Preise pro Stück berechnen sich nach zu strukturierendem Material, dessen Abmaße und der Komplexität der Werkstück-Geometrie. Welche Fertigungstiefe wir dem Kunden anbieten, hängt von dessen Wünschen ab. So sind z.B. bei einem planaren, DIN-A4 großen Blech aus Standardaluminium rd. 0,70 EUR pro Strukturierung (bei 1,0 Mio. Stück p.a.) akzeptiert.
Ergänzend kommt unser Produkt Anlagentechnik immer dann zum Einsatz, wenn der Kunde Anwendungen mit kleinen Stückzahlen hat oder Mobilität in der Anwendung vorausgesetzt wird. Als Sonderanlagenbau wird die Maschine auf die Ansprüche des Kunden konfektioniert und entsprechend nach Aufwand abgerechnet. So sind einfache, mobile Einheiten von 25,0 Tsd. EUR bis zu den Bahnschienenstrukturierungseinheiten im Projekt Endlosschienenverlegung mit >500,0 Tsd. EUR bepreist.
Vertrieb:
Bisher kamen unsere Kunden – namhafte Unternehmen der DACH-Region – mit Ihren Anwendungen auf uns zu. Ab 2024 werden wir unseren Direktvertrieb sukzessive aufbauen, um neben den bisherigen Großkonzernen insbesondere mittelständische Unternehmen zu akquirieren.
Trotz der breiten Einsatzmöglichkeiten unserer Technologie, fokussieren wir uns zunächst auf spezielle Anwendungen in der Mobilitäts- (Automobil, Luftfahrt, Schiene) und Baubranche. Hier ist der Anpassungsdruck am größten.
Auf Produktebene werden neben der Strukturierung von angefragten Körpern, Folien und Drähte im Vordergrund stehen. Erste bestehende Anfragen werden in 2024 abgearbeitet.
Markt und Zielgruppe
Die zukünftige Vertriebsstrategie von nascit konzentriert sich auf die Stärkung des Direktvertriebs, um unsere innovative Technologie gezielt auf dem Markt zu platzieren. Hierbei wird ein besonderer Fokus auf die Erschließung des deutschen Mittelstands gelegt.
Parallel dazu legen wir großen Wert auf den Ausbau unserer Präsenz in den sozialen Medien. Durch den gezielten Aufbau und die Pflege unserer Social-Media-Kanäle möchten wir die Aufmerksamkeit für unsere Lösungen steigern und potenzielle Kunden auf die Vorteile unserer Technologie aufmerksam machen. Beiträge in Fachzeitungen sollen dies flankieren.
Des Weiteren streben wir eine verstärkte Zusammenarbeit in Innovationsclustern und Kooperationen mit anderen Unternehmen an. Der Fokus liegt hierbei auf der gemeinsamen Entwicklung innovativer Lösungen für aktuelle Herausforderungen der Elektromobilität (Fahrzeuge müssen leichter, Batterien effizienter werden). Der Fokus liegt hier auf modularen Systemen die kundenbedarfsangepasste, elektrische Mobilität ermöglichen. Durch diese Kooperationen wollen wir nicht nur unser Netzwerk erweitern, sondern auch die Reichweite unserer Technologie erhöhen und neue Anwendungsbereiche erschließen.
Ziele und Kapitalverwendung
Dank der ersten Finanzierungsrunde über 2,5 Mio. EUR konnte
-
die interne Anwendungsentwicklung (“vom universitären Reagenzglas zur industriellen Anwendung“) überführt werden,
-
die Strukturierbarkeit aller Aluminiumlegierungsgruppen und Edelstähle entwickelt,
-
unsere Produktionsstätte gebaut und
-
wegweisende Entwicklungsprojekte, wie z.B. unsere Schwefel-Silizium-Batterie, umgesetzt werden.
Die aktuelle Finanzierungsrunde über 1,0 Mio. EUR wollen wir nutzen, um die operative Fertigung aufzunehmen. Ziel ist es, in 2025 die ersten Serienfertigungen für unsere Kunden zu starten und erste Anlagen abzusetzen. Hierfür ist es erforderlich, dass die Anlagentechnik – sowohl für die Eigennutzung als auch für den Absatz – als Prototyp entwickelt und gefertigt wird.
Das notwendige Labor wird eingerichtet, um die eingehenden Kundenanfragen auf Umsetzbarkeit zu prüfen und Kleinstserien und Muster abzuwickeln. Darüber hinaus werden die Mittel im Vertriebsaufbau und -start eingesetzt und um Betriebskosten zu decken.
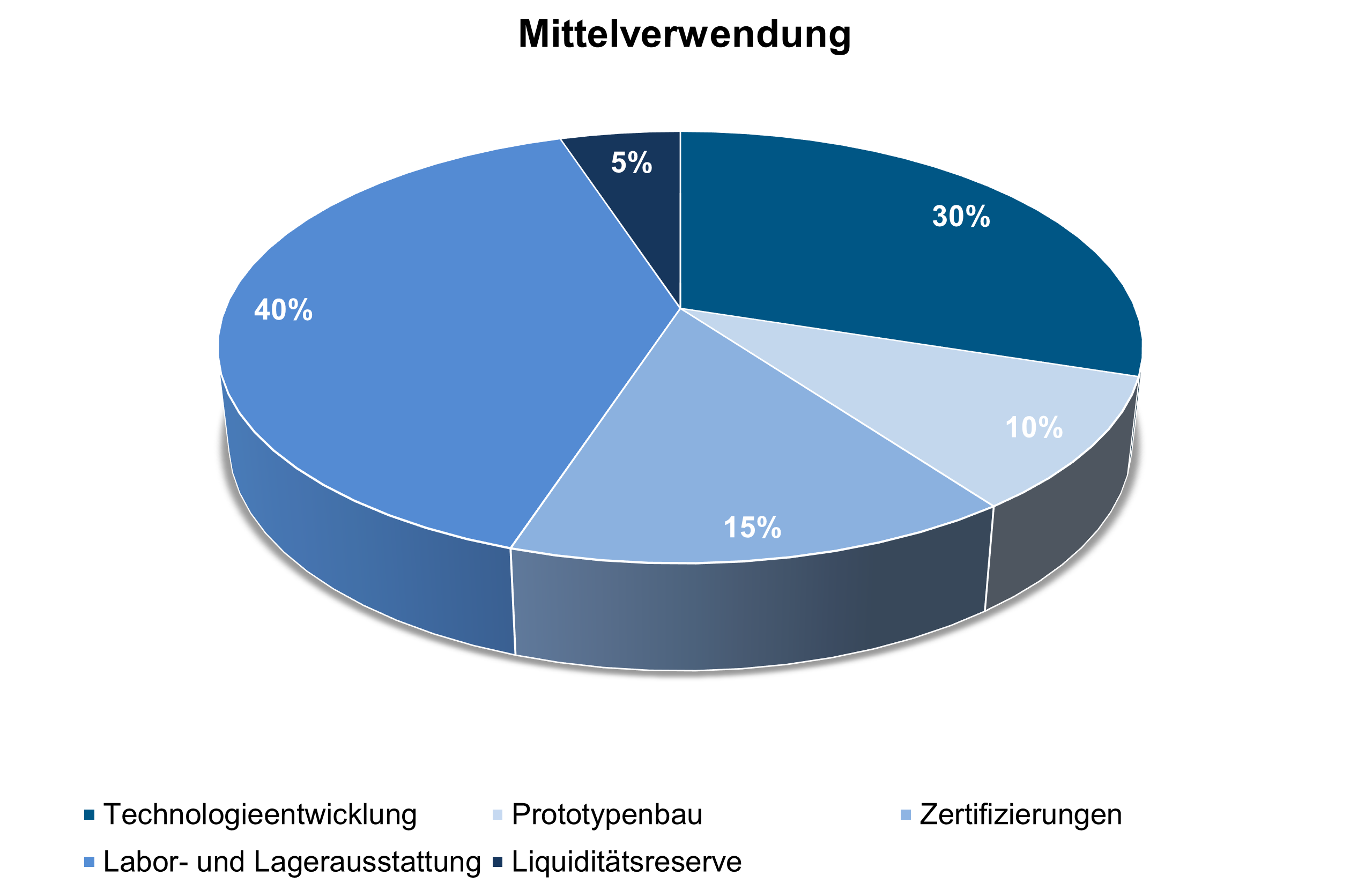
Bisherige Erfolge
Seit unserer Betriebsaufnahme Ende 2021 konnten wir international bekannte Kunden gewinnen. Mit diesen Kunden entwickeln wir in bezahlten Projekten Anwendungen für unser Nanoscale Sculpturing in diversen Produkten. Aktuell arbeiten wir daran, die erfolgreichen Ergebnisse der Projekte in Serienaufträge umzusetzen.
Als wichtigen Schritt hin zur industriellen Skalierung unseres Prozesses sehen wir die in 2023 erfolgreichen Tests an einer Demonstratoranlage zur Bearbeitung von Aluminiumfolien. Auf diesen Erfolg wollen wir in 2024 mit weiteren Analgentypen aufbauen und die Voraussetzungen für eine Serienproduktion ab 2025 schaffen.
Top Gründe für eine Investition
- Hohes Problemlösungspotential und hoher Kundennutzen: Wir lösen die Herausforderungen der klassischen Verbinungstechnik, indem wir mit unserem Nanoscale Sculpturing Verfahren Verbindungen zwischen Metallen und Polymeren ermöglichen oder deren Eigenschaften verbessern - unser Verfahren ermöglicht z.B. auch in der Batterietechnik erhebliche Vorteile (doppelte Effizienz, Wegfall von Selten-Erd-Metallen, nachhaltigere Herstellung, hohe Sicherheit (nicht brennbar)
- Nachhaltiges Investment: Innovative Batterietechnologie ist für nachhaltige Mobilität, Speicherung von erneuerbaren Energien etc. notwendig; Ressourcenschonung durch Leichtbautechnologie: Einsparung von Materialien und Gewicht (Dadurch effizienterer Betrieb bsp. von Autos oder Flugzeugen möglich)
-
Skalierbares Geschäftsmodell mit attraktivem Renditepotenzial in großen Absatzmärkten: Sehr großes Marktpotenzial (89 Mio. USD SOM / Serviceable Obtainable Market); Geringer Materialaufwand für die Bearbeitung der Oberflächen, einfache Bearbeitung von verschiedensten Bauteilen ohne große Anpassungen; Anwendungsmöglichkeiten der Technologie übersteigen aktuelle Use-Cases (Neue Anwendungen, aber auch Verbesserung bestehender Produkte möglich)
FAQ
Bei den genannten Branchen und Kunden gibt es lange Produktentwicklungs-Zyklen. Wie geht ihr damit um?
-
Bereits im Vorfeld des Serienauftrags werden durch Entwicklungsprojekte mit den Kunden Umsätze generiert
-
Anlagenvertrieb kann die Zeit bis zum Serieneinsatz von Großkunden überbrücken
-
Refinanzierung über öffentlich geförderte Projekte in der Zwischenzeit möglich
-
Der Fokus auf den genannten Use-Cases kam auf Grund der Kundennachfrage zu Stande und nicht, weil nascit sich diese Kundengruppe von vornherein ausgewählt haben
Besteht die Gefahr der Verzettelung durch die vielen Anwendungsmöglichkeiten eurer Technologie?
-
Die Anwendungsmöglichkeiten sind vielfältig, aber der Grundprozess bleibt gleich. Das betrifft sowohl die Anlagentechnik als auch die Serienfertigung
-
Klare Markteintrittsstrategie mit den Kundengruppen, die die Technologie aktiv nachfragen à sind zwar unterschiedliche Anwendungsfälle, aber bedarf lediglich geringfügigen Anpassungen bei nascit
-
Die Markteintrittskundengruppen haben einen sehr hohen Innovationsdruck
Sind Werkstücke, die aus einer Metall-Kunststoff-Verbindung bestehen, recycelbar?
-
Wir bearbeiten die Oberfläche des Metalls nur bis zu einer Tiefe von max. 30 µm. Das ist dünner als ein menschliches Haar
-
Durch die geringe Eindringtiefe unserer Bearbeitung können Verbindungen an der Grenzfläche zwischen Metall und Kunststoff mechanisch, z.B. durch Sägen, getrennt werden
-
Da Kunststoffe im Allgemeinen einen deutlich geringeren Schmelzpunkt als Metalle haben, lässt sich die Verbindung in einem Recycling-Prozess auch durch starkes Erhitzen lösen.